Guided Wave Pipeline Inspection System
TISEC specializes in the nondestructive testing of pipelines with long-range ultrasound.
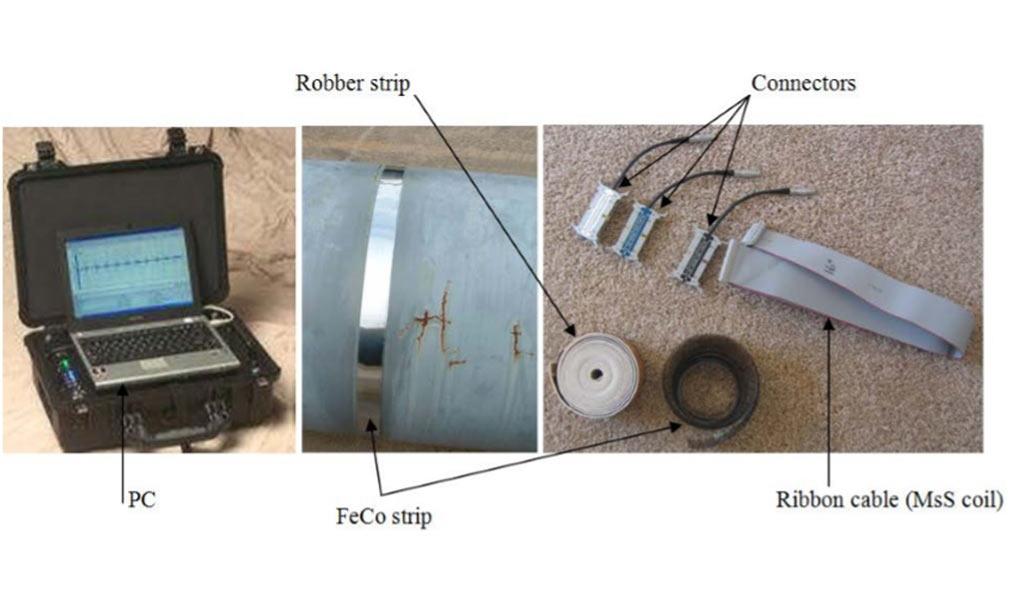
Inspection System
Under ideal conditions, the technology may be used to inspect up to 1000 feet (300 meters) of pipe from a single sensor position or up to 4000 feet (1.2 km) in one day. The actual inspection range depends on the type of pipe coating, degree of corrosion present in the pipeline, number of elbows, and whether the pipe is aboveground or underground. The technology may be applied to thin- and thick-walled pipe, with diameters ranging from 1″ to 60″, rapidly and economically. Download our pipeline inspection documentation
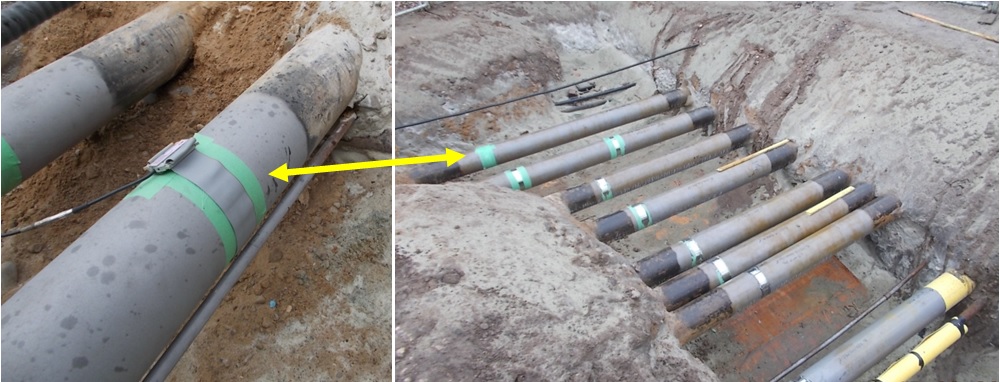

The reliable engineering data is used to assess exactly where your pipeline needs follow-up nondestructive or visual inspection.
Benefits include:
- Rapid screening of long lengths of pipe
- 100% of pipe wall is inspected
- Detection of corrosion in insulated and buried pipelines
How it Works
- The sensor is installed on the outer diameter (OD) of the pipeline.
- Long-range ultrasound is focused upstream and then downstream.
- Ultrasound is reflected back from pipeline corrosion.
- Corrosion is located with respect to the sensor location using the speed of sound in the pipeline tested.
- Corrosion severity is estimated in terms of cross-sectional area loss.
- Automatic report generation with reflector characterization and location.
Inspection Applications
- Transmission/distribution lines
- Refinery lines
- Offshore risers
- Tank farm lines
- Headers
- Storage sphere support legs
- Refrigeration lines
- Corrosion under insulation (CUI)
- Underground pipelines
- Pipelines under road crossings
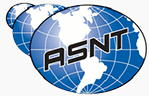
Our American Society for Nondestructive Testing (ASNT) certified inspectors have complementary training in fall protection, rope access, highway safety, railway safety, first aide, and confined space safety. With over 500 km pipelines tested to date, we have a proven track record for high quality nondestructive testing services and safety.
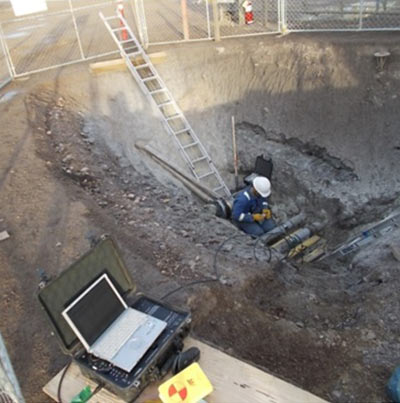