Compressed-Gas Cylinder Recertification
World government regulators are mandating stricter testing regimes for transportable compressed gas tubes and responsible major gas suppliers are showing due diligence in jurisdictions where their governments have not stepped in. In most jurisdictions, tubes and cylinders are required to be removed from their chassis or frame to undergo a 5-year hydrotest. Pneumatic on-the-trailer or in-situ acoustic emission testing recertifies the tubes for 5 years without having to dismantle the tubes from the trailer.
TISEC has been performing acoustic emission testing on these cylinders since the 1980’s both on trailers and in cylinder quads and on ground as well.
Scope of cylinder recertification services include:
- Tubes can be tested anywhere there is a means for pressurizing the tubes to 110% of their normal fill pressure.
- TISEC’s inspectors are certified to perform internal and external visual inspections as well prior AE testing.
- Routine rupture disk replacement and thread inspection can be performed.
Our AE method does not require disassembly of the trailer and avoids contamination and the need for cleaning and purging when water is used for the hydrotest because pressure for the test is applied using the gas normally transported in the tubes.
The trailers can be recertificated for 10 years if the acoustic emission testing is performed on tubes while they are on ground.
We also assist tube trailer owners and inspection companies in Australia and Indonesia in getting government approval for using the method instead of the conventional hydrostatic retest method.
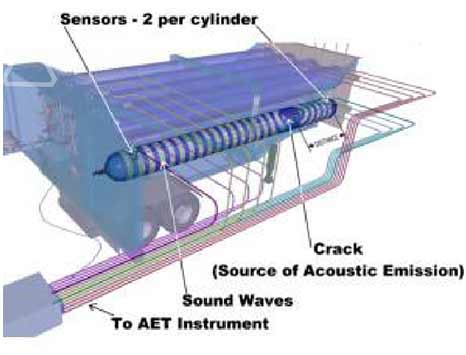
Acoustic Emission Equipment And Operators
Our Acoustic Emission equipment and operators are located overseas such as Australia, Indonesia area, Middle East, and North America.
After calibration, the tubes are loaded to 110% of the maximum operating pressure. During this loading period, active flaws, if present, in the cylinder’s wall will emit high frequency sound waves. These sound waves travel longitudinally in the cylinder until they are detected by the piezoelectric sensors located at each end of the cylinder. The relative time-of-flight of the sound wave at each transducer is used to locate the flaw longitudinally.
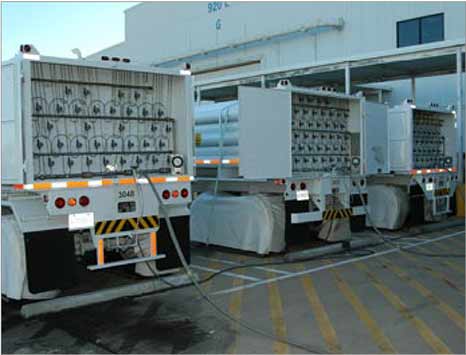
The Results
Our Acoustic Emission equipment and operators are located overseas such as Australia, Indonesia area, Middle East, and North America.
Reports are automatically generated using our STTAR® — System for Tube Testing And Reporting software. The software is used to track test pressure and acoustic events from active flaws in the cylinder’s wall. Acoustic events originating from active flaws in the cylinder are identified and located for follow-up ultrasonic testing. Results from up to 16 tubes may be viewed simultaneously.
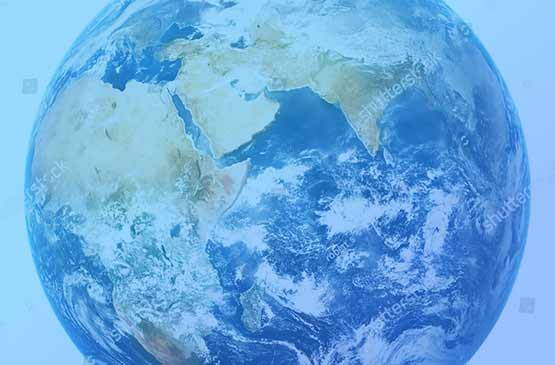
Government Acceptance
TISEC Inc. and TechKnowServ have official Transport Canada and United States Department of Transportation approval Permits to perform Acoustic Emission Testing on tube trailers in their respective jurisdictions:
- Transport Canada Special Permit TC-SU 5655
- Transport Canada Special Permit TC SU 6077
- USDOT,
- DOT-SP-14584
Based on TISEC’s experience and demonstrations, other jurisdictions have accepted Acoustic Emission testing of compressed gas cylinders in these applications: In 2002, TISEC Inc. performed several tube trailer tests in Sydney, Australia to demonstrate to the government that Acoustic Emission Testing was a safe alternative to the existing requirements. This study was performed with the cooperation of BOC Gas Australia, Air Liquide Australia and the Australian Gas Merchants Association leading to:
- Australian Standard 2337
And these cylinders are now routinely tested in Australia.
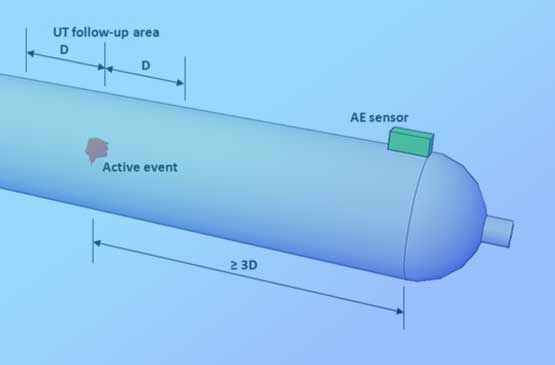
Follow-up UT Inspection
A follow-up ultrasonic inspection is required only if the AE inspection detects an active flaw during the loading period.
Our inspection procedure follows ASTM E 2223 Standard Practice for Examination of Seamless, Gas-Filled, Steel Pressure Vessels Using Angle Beam Ultrasonics.
These follow-up tests use 45° and 70° shear waves to locate and size detected flaws accurately.
Ultrasonic transducers are scanned longitudinally and circumferentially along the cylinder’s OD during this test.
Application
- Mining operations
- Bulk gas locations
- Shipping
- Oilfield operations
- Offshore
- Filling stations
- Multimodal facilities
Our Client Base
- Air Liquide Canada/USA/Australia
- Air Products
- BOC Gas Canada/Australia
- Praxair
- Linde
- Haliburton
- BJ Services
- Sanjel
- Ontario Power Generation
- Bruce Power
- FIBA Technologies
- FIBA Canning
- Saskatchewan Energy
- Soquip
- Junex
- Micron Industries
- Complete Truck Maintenance
- Environment Canada
- Specialty Trailer Leasing
- US Navy
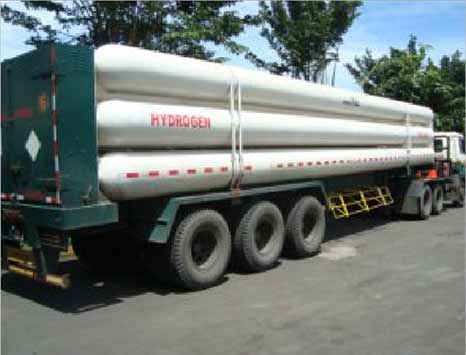
Our Services
No matter what quantity or size of tubes, TISEC will accommodate your needs.
We can manage your inventory and inspection program, or we can be “on-call”.
The TISEC Structural Insights® Group operates out of Canada, the United States and Indonesia. This experience and instrumentation base will make sure your tube and cylinder inspection needs are met throughout the Americas, Australia and New Zealand, the Asian continent and Africa.
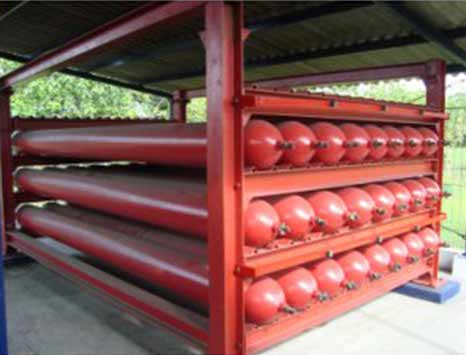
Qualified and Experienced Staff
Inspection staff is certified to the requirements of the American Society of Nondestructive Testing Standard ASNT SNT TC 1A.
With thousands of cylinders tested in North America and overseas we have a proven track record for high quality nondestructive testing services and safety.
Specifications
In addition to the details of our Special Permits for an equivalent level of safety granted by government regulators, TISEC also follows the following standards:
International Standards Organization, ISO 16148, Gas Cylinders-Refillable Seamless Steel Gas Cylinders-Acoustic Emission Testing (AT) for Periodic Inspection.
Compressed Gas Association, CGA C-18, Methods for Acoustic Emission Requalification of Seamless Steel Compressed Gas Tubes.
American Society for Testing and Materials, ASTM E1419, Standard Test Method for Examination of Seamless, Gas-Filled Pressure Vessels Using Acoustic Emission.
Original Works
The technology that is the basis of this approach was developed as a joint research program in Canada. The lead industries were TISEC personnel and Canadian Liquid Air. They were supported by a consortium of interested companies through the participation of the Hydrogen Industry Council. Government partners were the Dangerous Goods Directorate of Transport Canada, Energy Mines and Resources Canada, the National Research Council of Canada. Representatives of each of the above partners provided a steering committee for the project with participation of the United States Department of Transportation and National Bureau of Standards.