In-service Testing of Composite Cylinders
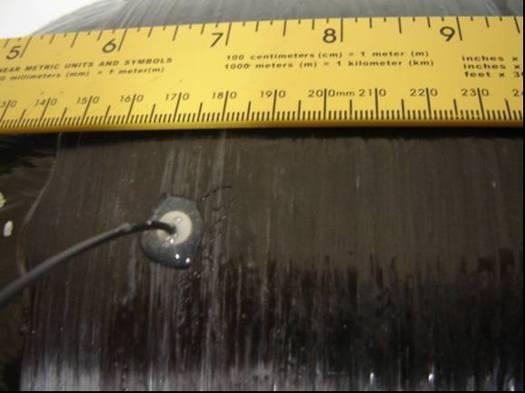
TISEC personnel have performed studies of the behavior of acoustic waves in Type III composite cylinders. A simple, low-profile ceramic piezoelectric disk was used in this application and it worked well. Input signal was sent to a transducer located on the top of the cylinder at the tangent point just inside the dome at one end, and received on the bottom tangent point at the other.
The interaction of the defects in these materials with transmitted ultrasound is complex and the effect on the transmitted wave may alter the waveform in ways other than simple amplitude changes. A significant change in cross-correlation coefficient between signals in undamaged materials and that obtained from a signal transmitted through a notch oriented parallel to the path between two sensors was obtained. A summary of the data obtained from a number of defects is shown in the table below.
Defect type | Defect size | Frequency (MHz) | Correlation Coefficient |
---|---|---|---|
Axial hole | 3.174 mm dia, 4.8 mm deep | 0.19 | 0.83 |
Axial impact | 20 x 20 mm observable surface damage | 0.19 | 0.44 |
Axial parallel notch | 25 x 2 x 2 mm | 0.19 | 0.83 |
Axial perpendicular notch | 25 x 2 x 2 mm | 0.19 | 0.68 |
Circumferential hole | 3.175 mm dia, 4.8 mm deep | 0.322 | 0.79 |
Circumferential damage | 20 x 20 mm observable surface damage | 0.322 | 0.69 |
Circumferential parallel notch | 25 x 2 x 2 mm | 0.322 | 0.93 |
Circumferential perpendicular notch | 25 x 2 x 2 mm | 0.322 | 0.85 |