Amusement Park Rides Non Destructive Inspection
TISEC Inc. provides non-destructive inspection to the amusement park industry. It is important to verify the condition of amusement ride components such as axles, bogies, pivots, chassis, lap bar parts and other structural components to ensure safety and uninterrupted service during times of heavy use.
The devices are subjected to two cycles of loading at loads two times their rated capacity while being monitored for acoustic emission activity, which can be an indication of fatigue.
The NDT and inspection services offered are Visual Inspection (VI), Magnetic Particle Testing (MT), Liquid Dye Penetrant Testing (PT) and Ultrasonic Testing (UT).
- Visual Inspection is the first tool in the inspection of any structure or component. Prior to any further NDE, a thorough visual inspection will be carried out. This inspection will reveal corrosion, damage and wear much more readily than other methods and can indicate where other investigative methods should be targeted. Over 90% of defects are found by the naked eye.
- Magnetic Particle Inspection is performed in accordance with ASTM E 790. The most common and widely-used method of NDE is magnetic particle testing (MT). The technique employs the nature of magnetic fields to identify potential defects. In magnetised materials, the magnetic field tends to travel within the solid material. When an applied field meets a crack or other defect, it will tend to ‘jump’ across the crack. Inspection engineers use magnetic ink to pick up this ‘jumping’ mechanism and hence identify a flaw.
- Liquid Dye Penetrant Inspection is performed in accordance with ASTM E 165. Dye or liquid penetrant inspection is a widely applied to locate surface-breaking defects in all non-porous materials (metals, plastics, or ceramics). Penetrant may be applied to both non-ferrous and ferrous (magnetic) materials, but for inspection of ferrous components magnetic particle inspection is preferred for its sub-surface detection capability. PT is used to detect casting and forging defects, cracks, and leaks in new products, and fatigue cracks on in-service components.
- Ultrasonic Inspection is performed in accordance with ASTM E 164. Ultrasound is used to find deep metal flaws (ex. cracking and inclusions) and to check thicknesses of parts.
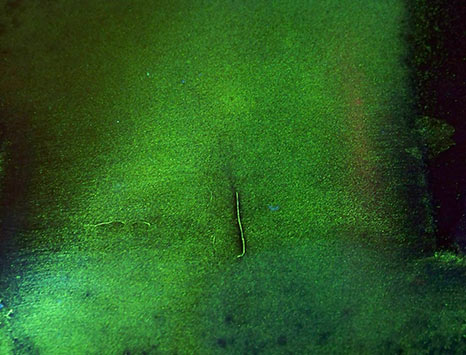
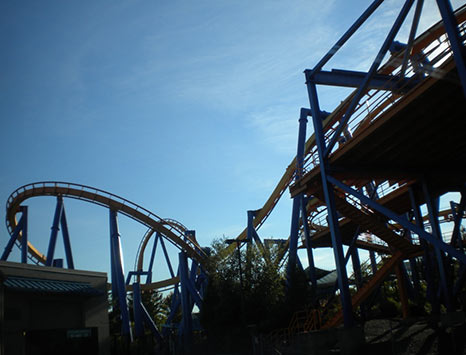
In addition to flaw detection, TISEC will also re-qualify repairs. TISEC’s personnel are capable of performing manufacturer-required inspections as well as innovative and high tech inspection methods such as:
- Advanced ultrasonic rail track inspection inspect coaster track for defects in the head region
- Guided wave tubing inspection inspect tubular track and sections for cracking and corrosion.
- Phased array ultrasonic inspection is an advanced ultrasound technique that has the ability to sweep inspection angles to maximize the visible inspection area in parts with complicated geometry.
- Remote operated video inspection is for visually gaining access to areas that are hidden or otherwise inaccessible for other NDT examinations.
- Bolt Inspection is performed to ASTM standards. Bolt inspection reveals the condition of in-use hardware and will also determine if the bolts and nuts are properly torqued.
TISEC provides owners with technical inspection reports that can be filed with state inspectors or other governing bodies.
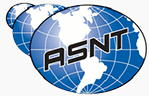
Our American Society for Nondestructive Testing (ASNT) certified inspectors have complementary NDT and safety training. With over 300 tanks tested to date, we have a proven track record for high quality nondestructive testing services and safety to meet all of your needs.
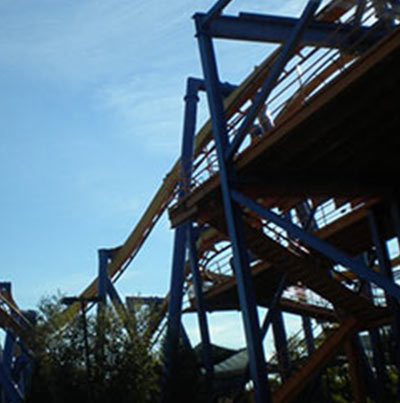